Контроль продольного разрыва конвейерной ленты
Важность контроля продольного разрыва ленты конвейера
Ленточные конвейеры широко используются для транспортирования сыпучих и кусковых материалов: руды, угля, щебня и т.п. Конвейерная лента, изготовленная из армированной резины является главной частью конвейера. Ее стоимость составляет около 40% от стоимости всего конвейера.
Продольный разрыв конвейерной ленты в процессе транспортирования материала влечет за собой разрушительные последствия и дорогостоящие затраты на их устранение. Помимо ремонта или замены самой ленты, потребуется проведение работ по разгрузке конвейера, ведущих к существенным затратам, к которым добавляются экономические потери, связанные с остановом технологического процесса.
Угроза продольного разрыва конвейерной ленты, особенно в условиях жесткой эксплуатации, существует всегда, в связи с чем технологиям обнаружения продольного разрыва уделяется повышенное внимание. Ниже приведена диаграмма, иллюстрирующая соотношение основных причин продольного разрыва на основании исследования 29 случаев разрыва, проведенного компанией «Угольно-минеральный терминал порта Кингдао» в период с 1999 по 2009 гг.
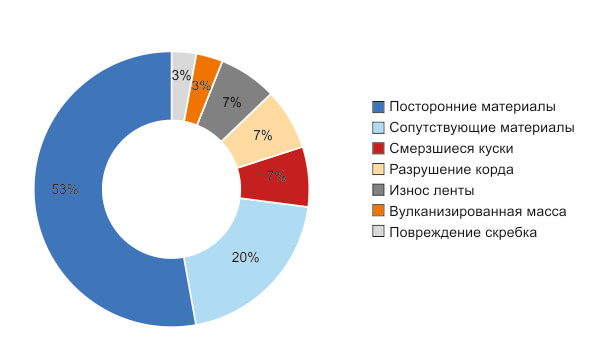
Как показано, большая часть причин — 53 и 20 процентов обусловлена включением посторонних и сопутствующих материалов, травмирующих ленту. Посторонние материалы это острые куски железа, камня, попавшие на ленту конвейера извне. Сопутствующие материалы — инородные включения (острые куски камня и т.п.) в составе транспортируемой массы.
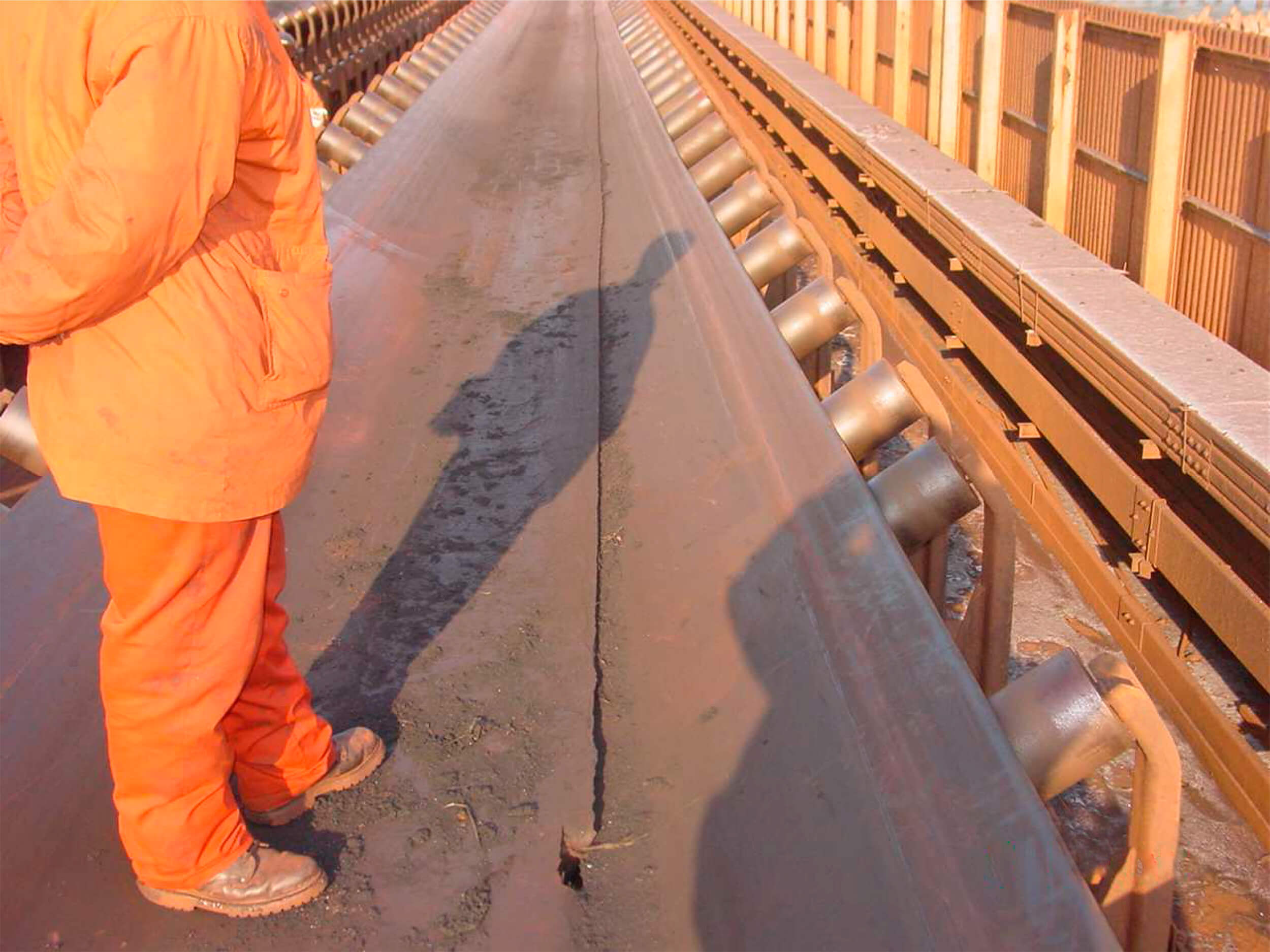
Снимок демонстрирует очевидный признак продольного разрыва — анормальное сужение ленты из-за нахлеста, а также, второй признак — протрузию ленты внутрь в месте прорыва посторонним объектом. Помимо сужения, отмечены также факты анормального расширения ленты в результате расклинивания продольного разрыва кусками материала.
![]() |
В настоящее время не существует доступных способов обнаружения названных причин, позволяющих предупредить продольный разрыв, поэтому основное внимание уделяется технологиям и методам, способным на ранних стадиях обнаруживать продольный разрыв, уже, после появления такового. Исследовательская задача в данной области сводится к изучению признаков продольного разрыва и технических возможностей обнаружения возникновения этих признаков. |
- Контроль целостности ленты с помощью поверхностных звуковых волн Релэя.
- Контроль целостности ленты со встроенными электромагнитными контурами с помощью специализированной техники, основанной на измерении индукции.
- Обнаружение просыпи материала на холостую ветвь конвейера.
- Контроль сбора просыпи в специальном лотке.
- Обнаружение протрузии ленты с помощью поперечного троса.
- Измерение ширины ленты с помощью ультразвуковых датчиков.
Первые два метода, безусловно, являются самыми эффективными, позволяющими быстро обнаружить разрыв и локализовать его на ннаименьшем участке, но и самыми дорогими, при том, что метод, основанный на измерении индукции требует применения специальной конвейрной ленты со встроенными электромагнитными контурами.
Методы 3, 4 и 5 могут быть реализованы с помощью простого и недорогого оборудования, но они допускают значительное распространение разрыва.
![]() |
Метод ультразвукового измерения ширины ленты является компромисом между дорогими методами 1-2 и простыми 3-5. В сравнении с «простыми» методами ультразвуковое измерение способно раньше обнаружить разрыв, при значительно меньшей стоимости оборудования, нежели, того, что используется в методах 1-2. |
Сочетание ультразвукового и одного их простых «механических» методов позволяет существенно повысить надежность и чувствительность обнаружения разрыва конвейерной ленты.
Пост измерения ширины ленты на базе двух ультразвуковых датчиковИдея обнаружения разрыва основывается на непрерывном дифференциальном измерении ширины ленты с помощью двух ультразвуковых аналоговых датчиков, расположенных по обе стороны ленты и «нацеленных» на ее края. Дополнительным преимуществом метода является возможность контроля смещения ленты.
Благодаря применению ПЛК, аналого-цифровому преобразованию и программированию, пользователь не обременен какими либо жесткими требованиями по механической установке датчика. Необходимо лишь учесть возможную критическую амплитуду смещения ленты и, насколько позволяет диапазон датчиков, установить их на разумном удалении от краев ленты.
Перед пуском конвейера в эксплуатацию для настройки программы необходимо произвести «сканирование» ленты путем как минимум одного полного оборота с целью определения допустимой погрешности из максимальной измеренной амплитуды колебания краев по всей длине ленты и средних значений измерений каждого датчика.
Средние значения сохраняется в ячейках памяти ПЛК и являются эталонными, их сумма соответствует ширине исправной ленты. Контроль целостности и смещения ленты производится на основании текущего контроля ее ширины и положения путем сравнения текущих измерений с эталонами в пределах допустимой погрешности.
Аварийная ситуация выявляется по следующим признакам:
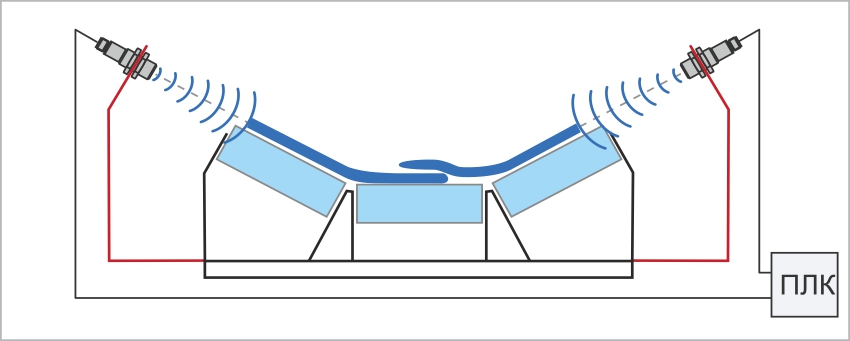
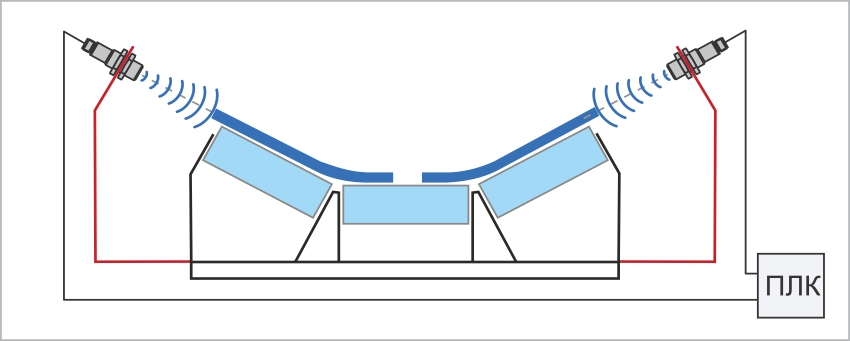
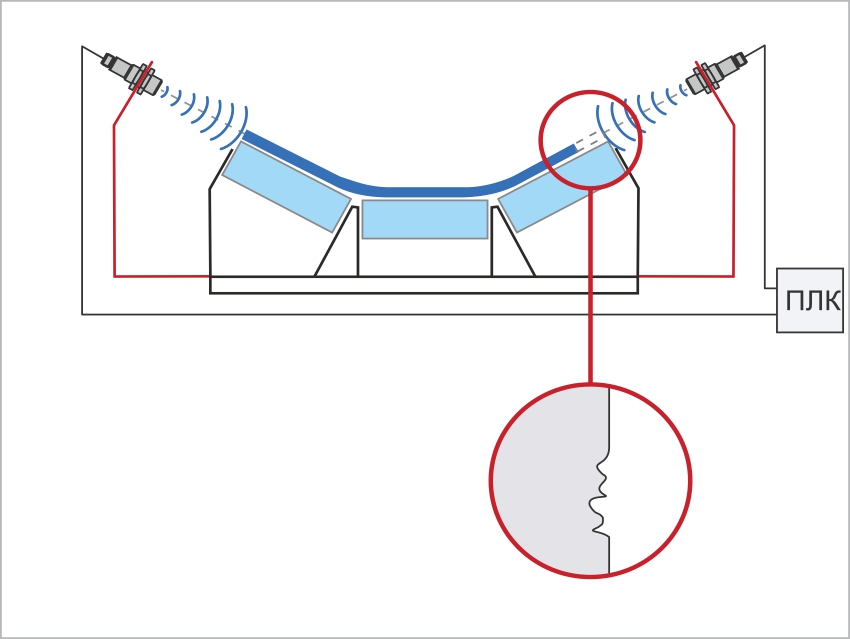
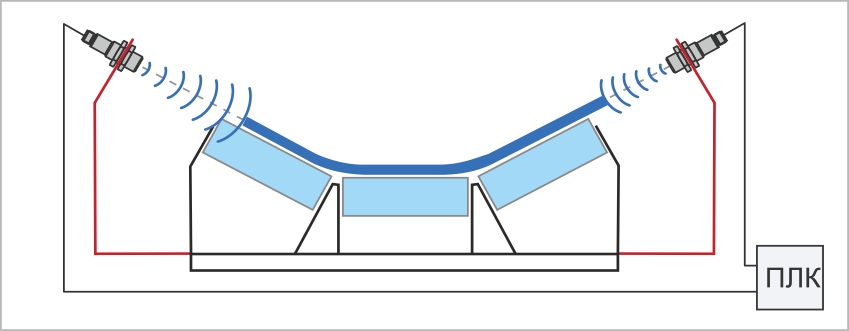
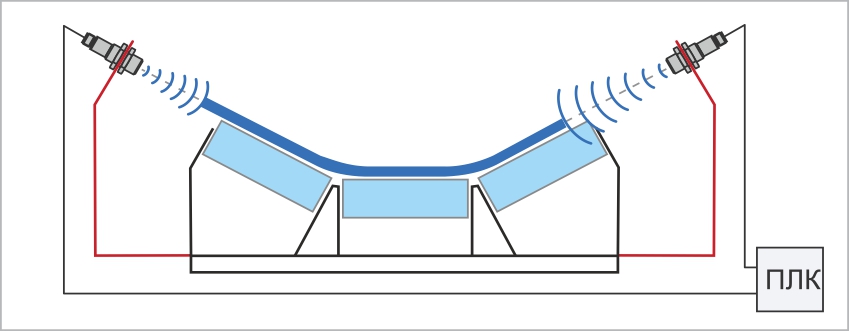
Пост измерения включает:
1) Ультразвуковые датчики USSA A89B-43P-1000-LZ в количестве 2 шт, с диапазоном 1000 мм и аналоговым выходом 4-20мА (0-10В)
Ультразвуковой датчик USSA A89B-43P-1000-LZ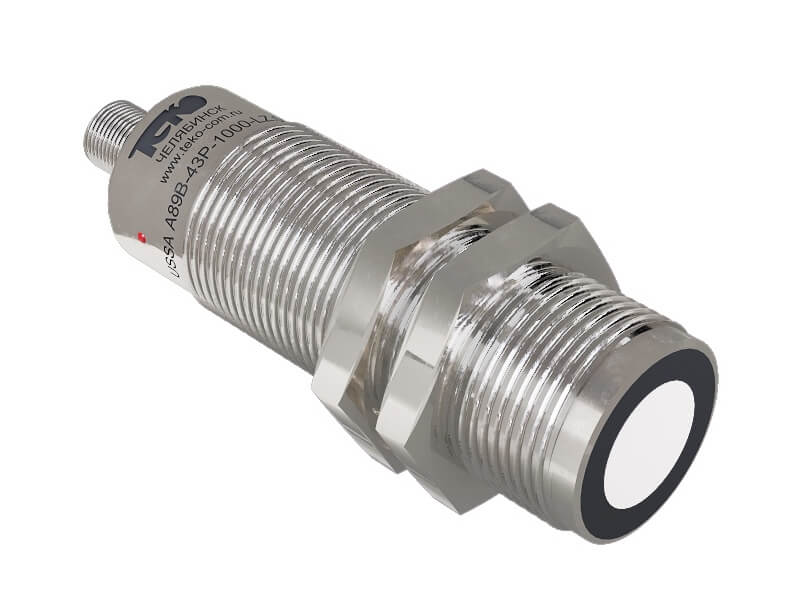
Запросить цену
Технические характеристики ультразвукового датчика USSA A89B-43P-1000-LZ
Формат, мм | M30x1?5x90 |
Частота ультразвуковых импульсов | 200 кГЦ |
"Слепая зона" | 0...150 мм |
Зона чувствительности | 150...1200 мм |
Коэффициент пульсацяий напряжений питания | 12...30 B DC |
Собственный ток потребеления, не более | 40 мА |
Тип выхода | токовый выход (4-20 мА) или выход по напряжению (0-10 В) |
Сопротивление нагрузки:
- токовый выход
- выход по напряжению
|
< 500 Ом
> 10 кОм
|
Максимальная емкость нагрузки | 0,02 мкФ |
Время готовности датчика после подачи питания, не более | 1000 мс |
Категория применения | DC13 |
Максимальная частота циклов оперирования | 5 Гц |
Защита от неправильного подключения питания | Есть |
Защита от короткого замыкания в цепи нагрузки | Есть |
Индикация состояния | Есть |
Диапазон рабочих температур | -15°С...+65°С |
Степень защиты по ГОСТ 14254-2015 | IP65 |
Материал корпуса | Полимер "РВТ" |
Материал гаек | Текамид |
Присоединение | Кабель 4х0,5 мм2; L=2м |
2) Контроллер датчиков на базе программируемого реле со следующими функциями:
- прием сигналов от датчиков по двум аналоговым каналам
- начальная калибровка системы — измерение и запоминание расстояния до краев ленты
- калибровка во время холостого прогона ленты — вычисление допусков измерения
- установка таймера не критического смещения
- непрерывный анализ ширины ленты на основе измерения расстояний до краев ленты
- непрерывный анализ бокового смещения ленты
- анализ частоты аналоговых сигналов — пульсация сигнала может указывать на задир края ленты
- переключение выходного реле НО, подключенного к цепи предупреждения СУ в случае обнаружения не критического смещения ленты, запуск таймера
- переключение выходного реле НО в случае задира края ленты
- сброс таймера, если не критическое смещение прекратилось — лента вернулась в нормальное положение благодаря системам стабилизации
- переключение выходного реле НЗ, подключенного к цепи аварийного останова в случае анормального сужения или расширения ленты, критического смещения или истечения таймера не критического смещения
- управление обогревом датчиков
- включением местной сигнализации.
- Дистанционное обнаружение – отсутствие контакта с лентой конвейера, возможность вести обнаружения из безопасного места
- Высокая точность изменений - несколько миллиметров
- Решение нескольких задач: контроль смещения, обнаружение продольных разрывов, обнаружение повреждения кромки
- Возможность расширения задач, благодаря применению ПЛК, например: контроль износа ленты
- Простота установки и настройки
- Индифферентность к пыли и грязи.